Backward Vertical Integration Strategy
There are two ways in which businesses vertically integrate. When a business extends its operational activities in the direction of its customers, it is said to be forward vertical integration. However, if a business extends back through its supply chain to control early-stage inputs, it is called backward vertical integration.
Integrating backward or forward has its advantages and some companies even decide to become completely integrated by integrating both ways. That is, the company takes charge of all the stages in its supply chain; from producing its own raw materials to manufacturing to selling directly to its end users.
However, compared to integrating forward, backward vertical integration gives a business more control over its process. In this article, we will be discussing the advantages and disadvantages of backward vertical integration and some real-life examples of companies using this strategy.
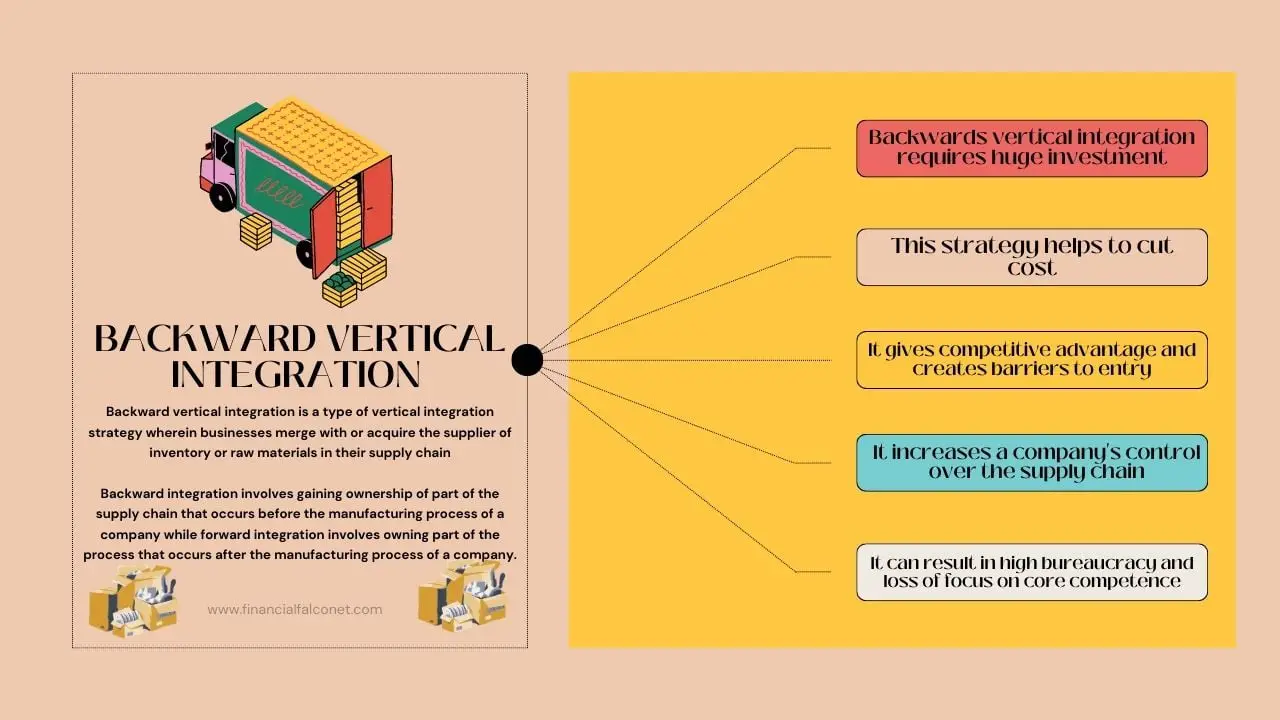
Related: Horizontal Integration Examples of Companies
What is backward vertical integration?
A lot of companies employ vertical integration strategies as a means to take over a portion of their supply chain. The supply chain of a company starts with the delivery of raw materials from a supplier and ends with the sale of the finished product to end consumers. Hence, implementing a backward vertical integration strategy involves a company expanding its role to perform the tasks that were formerly carried out by businesses up the supply chain.
See also: The Supply Chain Issues of Nike
That is, the company acquires or merges with another company that supplies the raw material, inventory, or services that it needs for its production. Alternatively, the company can also establish its own subsidiary to perform the task of the suppliers. Hence, backward vertical integration involves gaining ownership of part of the supply chain that occurs before the manufacturing process of a company while forward integration involves owning part of the process that occurs after the manufacturing process of a company.
Companies may consider integrating backward for technological expertise or efficiency enhancement. A typical backward vertical integration example would be a bakery purchasing a wheat farm or a wheat processor. With backward integration, the bakery becomes an owner of its supplies rather than a customer that makes purchases from suppliers.
This can enable the bakery business to gain market share in its industry by getting a limited supply of its raw materials (wheat) before its competitors. In times of delays from supply chain disruption, this business will have an advantage over its competitors as it will still be able to produce finished goods and deliver them sooner and more consistently to customers.
A backward vertical integration strategy can be considered by companies that have difficulties obtaining raw materials on time for a reasonable cost. Also, if a business is experiencing financial stability issues or problems with its supplier quality, it can investigate between using backward integration or switching suppliers.
See also: Telstra’s Vertical Integration Strategy and Examples
Backward vertical integration examples
- Amazon opening its own publishing division in 2009 is a backward vertical integration example because by integrating backward, it expanded its business to become both a book publisher and a book retailer; by turning into a publisher, Amazon integrated the role of its suppliers into its business.
- McDonald’s integrates backward by being the source of its products and setting up its own manufacturing plants to acquire the raw materials that it uses for the preparation of its eatables; this fast food grows its own potatoes, processes the meat it uses itself, and transports its own raw materials.
- Tesla also uses backward vertical integration by manufacturing its own electric motors and producing the batteries it uses for its electric cars, rather than using external contractors; it also has its own supercharger networks to charge the car batteries and creates its own software and firmware. Tesla’s vertical integration strategy has given it good control over the timeliness, cost, and quality of its production processes.
- Netflix is one of the backward vertical integration examples because it started as a DVD rental company that distributed the films and TV shows created by others, but later integrated backward by creating its own original content; now, Netflix streams more original content and reduces its dependence on film studios and their licensing.
- IKEA, a Swedish furniture and home accessories giant, is an example of backward vertical integration; this furniture company integrated backward by purchasing 83,000 hectares of forests in Romania in order to take charge of the supply of its timber.
Read also: Disadvantages of Vertical Integration
Advantages of backward vertical integration
- Backward vertical integration increases control over the supply chain
- This strategy helps to cut cost
- It provides better efficiency in the manufacturing process
- Differentiation of product from competitors
- This strategy gives backward integrated companies a competitive advantage and creates barriers to entry
Here are some advantages of backward vertical integration:
Backward vertical integration increases control over the supply chain
Companies can efficiently increase their control over their supply chain by integrating backward. By merging or acquiring their suppliers, companies can control the production or supply of raw materials and ensure the quality of raw materials used in the production of the end product. Also, by integrating backward, a company secures the supply of its material. Backward vertical integration ensures a company receives adequate supplies of raw material when required without bothering about it being sold to other competitors or not being manufactured by the suppliers after placing an order.
This strategy helps to cut cost
One of the major advantages of backward vertical integration is that it helps in cost-cutting. When goods are sold from one business to another, there is always a markup in the supply chain. By implementing backward vertical integration, a business can integrate its raw material supplier into its business which can help cut the markup costs, transportation costs, and other costs involved in the supply process.
It provides better efficiency in the manufacturing process
While cutting costs, backward vertical integration also helps to enhance efficiency in the manufacturing process. When a business has control over the supply side of the chain, it can control which raw materials to supply or produce, when to supply or produce, and how much to supply or produce them. This improves the efficiency of the manufacturing process because the business saves cost on the raw material that would have been unnecessarily wasted due to over purchase.
Differentiation of product from competitors
Companies benefit from using backward vertical integration because it tends to maintain the differentiation of their product from their competitors. Backward vertically integrated companies gain access to the production units and distribution chain and therefore, tend to market themselves differently from their competitors. By integrating backward, a company holds the production capacity internally instead of sourcing it from the market. This, therefore, improves its ability to meet customers’ demands and provide customized products.
This strategy gives backward integrated companies a competitive advantage and creates barriers to entry
Companies can integrate backward to keep competition out of the market. Take, for instance, Company A and Company B are strong competitors in the same industry but Company A later acquires a major supplier that supplies materials to them. This will stop the supply of materials to Company B from this major supplier and also create barriers to entry for new competitors.
Furthermore, integrating backward can also help Company A gain access and control of patents, technology, and other important resources that were only held by the supplying company, thus giving it a competitive advantage over Company B.
See also: Vertical Integration Benefits
Disadvantages of backward vertical integration
- Backwards vertical integration requires huge investment
- It can result in higher costs
- It can result in high bureaucracy and loss of focus on core competence
Here are some disadvantages of backward integration:
Backward vertical integration requires a huge investment
Integrating backward will require huge investments and as a result, some companies resort to taking large amounts of debt in order to purchase a supplier or production facility. This will be an extra burden on the company’s balance sheet, regardless of the cost savings realized from integrating backward. This is a major drawback because, in the future, the debt added to the company’s balance sheet may prevent the company’s bank from approving it for additional credit facilities.
It can result in higher costs
Costs reduction is not always the case in backward integration because integrating backward can result in higher costs when efficiency is reduced due to a lack of supplier competition. Hence, in some cases, it can be more cost-effective and efficient for companies to depend on independent suppliers and distributors.
Also, backward vertical integration can be a disadvantage if a supplier can achieve lower costs as it increases the number of units produced (economies of scale). In such instances, the supplier is in a better position to provide input goods at a lower cost compared to when a manufacturer integrates backward to become a producer/supplier of the input goods.
Therefore, backward integration would be an extra burden on a company and result in higher costs if the company cannot achieve the economies of scale that an independent supplier can achieve. This is one of the major disadvantages of backward vertical integration.
It can result in high bureaucracy and loss of focus on core competence
Backward integration requires acquiring the supplier which means the workforce of the supplier is acquired as well and integrated into the parent company. This causes the company to increase in size. The drawback of this increase is that, in some cases, when a company becomes too large, it may be difficult to manage. This can even cause the company to lose focus on what made it profitable (its core competence) before the acquisition.
Also, there is also a tendency for high bureaucracy, as new policies are brought in for the employees. The company’s administrative procedure can become excessively complicated resulting in a bureaucratic culture in the company.
Related: