Process Costing System: Examples, Methods, and Steps
Process costing system is an accounting method usually used by manufacturing companies that mass produces very identical products or units of output. This costing system is used when the costs of producing each individual unit are very similar, and it is difficult to track the costs for each individual unit throughout the production process. In this article, we will discuss the process costing system examples, methods, and steps.
Examples of companies that use process costing methods would include processed food companies that make millions of identical packages of edibles and oil companies that produce millions of gallons of fuel. Such companies use several different methods of process costing such as weighted average costing, standard costing, or first in, first out (FIFO) costing to determine the cost of one unit of output. We are going to discuss how these methods are used in a process costing system but first let’s have an understanding of what a process costing system is.
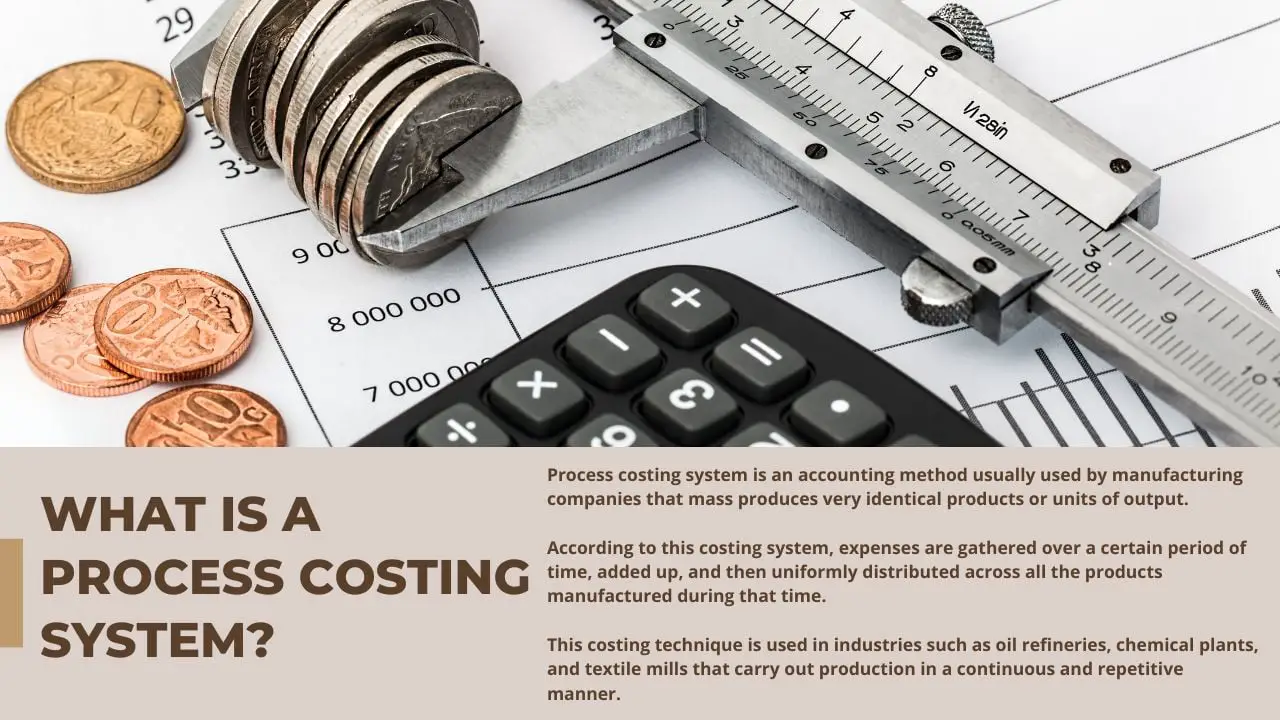
Read also: Predetermined Overhead Rate (POHR): Formula and Calculation
What is process costing system?
A process costing system is used in industries such as oil refineries, chemical plants, and textile mills that carry out production in a continuous and repetitive manner. When using this costing system, it is assumed that the production process is homogeneous and that all products go through the same sequence of production stages. Hence, a process costing system is used to estimate product costs in manufacturing industries.
Definition of process costing in accounting
In accounting, process costing is defined as an accounting system that is used to assign manufacturing costs to each unit produced. In this system, the cost of direct materials, direct labor, and overhead costs are accumulated separately and an average cost is assigned to each unit produced. That is, the costs associated with each step of the production process are summed up and divided by the number of units produced in order to arrive at the cost of each unit produced.
Process costing formula
In a process costing system, an item cost is determined by tracking the cost of each stage in the production process, rather than tracking the costs for each individual item. The cost of all the stages in the production process is tracked and added up to get the total cost which is then divided by the number of items to get the cost per unit.
That is, the cost of each unit is calculated in a process costing system by dividing the total costs incurred by the company during the production period by the number of units produced. Hence, the formula for process costing is expressed as:
Cost per unit = Total cost of a process / Total number of units produced during the given period
For example, to get the cost per ream of paper in a paper company, the total cost of each stage involved in the process of turning wood pulp into reams of paper is calculated and then divided by the number of reams produced.
Objectives of process costing
One of the main objectives of a process costing system is to provide a manufacturing company with a clear picture of the costs associated with each unit that it produces; this can be used to make decisions about production levels, pricing, and other aspects of the company’s operations. Another objective of the process costing system is to monitor profit margins. A slight change in the process costs of a company that sells products in high volume and operates with narrow profit margins can make a big difference to its profit. Hence, using a process costing system enables such companies to pay attention to the cost of each stage of production and target specific departments for improvement.
Inventory control is also one of the objectives of process costing. A company, depending on its kind of business, may be required to report inventory to the Internal Revenue Service (IRS) for tax purposes. This can be a difficult task for large companies that produce thousands or millions of products. Nonetheless, a process costing system can be used to simplify it wherein each produced item is valued and each department tracks associated costs, like the cost of materials purchased.
A process costing system also aims to ensure uniformity in reporting. By using this system, each department tracks its own costs and all those costs will be rolled up to arrive at a total cost to produce a specific number of products. Since all the expenses have to be summed up in a process costing system, they have to be reported in the same manner which brings about uniformity to reports and makes tracking costs over time easier.
Read about: Tangible Book Value: Formula and Calculation
Steps in process costing system
- Analyze inventory to determine the amount of inventory at the beginning of the period
- Calculate the equivalent units to account for the number of unfinished items at the end of the period
- Calculate applicable costs
- Divide the total cost by the number of units to determine the cost per unit
- Allocate costs to complete and incomplete products
The homogeneous products produced in the chemical, oil, timber, textile, or food processing sectors cannot be identified from one another because such identical items usually pass through several stages during the course of production. Hence, a process costing system is used to allocate costs to an individual unit after a process of mass production.
In order to estimate the cost of producing each individual unit accurately, process costing takes into account, at the start and end of each period, the items that have completed the production process as well as the work-in-progress items (i.e. items that have started the production process but has not been completed). Here are the 5 steps in the process costing system:
Analyze inventory to determine the amount of inventory at the beginning of the period
The first step in the process costing system is to analyze inventory. A company has to analyze the flow of items during the production period to determine the amount of inventory at the beginning of the period. The number of items that were started during the period, the number of items that were completed and transferred out, and the number of items that were incomplete at the end of the period have to be determined and recorded.
Calculate the equivalent units to account for the number of unfinished items at the end of the period
The next step in a process cost system is to calculate the equivalent units in order to account for items that are unfinished at the end of each period. For this step, the number of incomplete units at the end of the period is multiplied by a percentage that represents their progress in the production process. For instance, if there are 2,000 units of inventory still in progress that are 75% complete, it is assumed that for process costing purposes, these unfinished 2,000 units are equivalent to 1,500 units (i.e. 2,000 x 75%).
Calculate applicable costs
Calculating the applicable costs is the next step in the process costing system. This involves summing up the total costs for all production stages, such as the direct materials and conversion costs. In a process cost system, the direct expenses and production overhead are calculated for every one of the stages of production.
Companies usually break down the costs calculated for every one of the stages of production into direct materials and conversion costs. Direct materials are the materials used at each stage while conversion costs include the expenses that are associated with the production process such as labor costs and the overhead costs in the production process.
In many companies, each stage of the production process is usually handled by a different department. Hence, each department prepares a report that includes the three elements of process costing which are the department’s direct materials, direct labor, and manufacturing overhead. The company then combines these reports to analyze the applicable total cost of the product.
Divide the total cost by the number of units to determine the cost per unit
The next step is to calculate the per-unit cost. The total cost of the product that is arrived at at the end of the period is allocated according to the number of completed and unfinished products (equivalent units). This is done by dividing the total cost of the products by the number of units.
Let’s assume, a manufacturing business completed 4,000 products and has another 1,000 units halfway through production, the total costs would be divided by 4,500 units [i.e. 4,000 + (1,000 x 50%)]. If the total cost calculated across all departments to produce these units was $16,875, it means that the cost per unit will be determined by simply dividing the total cost of $16,875 by the 4,500 number of units. This will arrive at $3.75 per unit produced.
Allocate costs to complete and incomplete products
Next is to allocate costs for the completed and incomplete products to the corresponding accounts in order to determine how much money is tied up in the current work-in-progress products. Using the example above, since the 1000 units in progress are equivalent to 500 units and it costs $3.75 to produce each unit, it means the complete product inventory cost will be $15,000 (4,000 x $3.75) while the work-in-progress inventory cost will be $1,875 (500 x $3.75).
The cost allocated per unit is recorded on the balance sheet in the inventory asset account. Then, when the products are eventually sold, the cost is shifted to the cost of goods sold account on the income statement.
See also: Profit Margin Ratios-Formulas and Calculations
Methods of process costing
- Weighted average costs method
- Standard costs method
- First in, first out (FIFO) method
In a process costing system, there are three different ways to calculate costs. This can be done either using the weighted average method, standard costing method, or the first-in-first-out (FIFO) method. It is usually good accounting practice to carefully select the process costing method that best meets a business’s needs.
Weighted average costs method
This process costing method is the simplest method for calculating cost. When using this method, the total number of units completed and transferred out is added to the equivalent units of work-in-progress to get the total number of units at the end of the period. Then, all the costs for the current period are summed up and divided by the total number of units. This method is used for cases where there are slight fluctuations in costs from period to period or where there is no standard costing system.
Standard costs method
This process costing method is similar to the weighted average costing method, only that it uses an estimated standard cost for each process stage rather than actual costs. Companies usually make use of this method in a process costing system when it is time-consuming or not convenient to collect the current information about the real costs.
There are situations whereby companies manufacture a broad mix of products and find it difficult to accurately assign actual costs to each type of product; in such instances, using standard costs can be very useful. After a production run is finished, the total costs that are accumulated based on standard costs are then compared to the actual total costs, and the difference between them is added to a variance account.
First in, first out (FIFO) method
This process costing method is the most complicated process costing method compared to the weighted average and standard cost methods. In a situation whereby costs change significantly from one period to the next, the FIFO method can be used to get a more precise product costing.
That is, the FIFO costing method is used when changes in product costs from period to period are so significant to an extent that the management team needs to know the new costing levels in order to re-price products appropriately or determine if there are internal costing problems that need resolution.
When using this method, layers of costs are created; one for any units of production that were started in the previous production period but is yet to be completed, and another layer for any units of production that are started in the current period.
See also: Adjusting entry for inventory
Process costing system examples and solutions
Process costing system is used in circumstances where the units of product are homogenous. Examples of companies that use process costing systems include Pittsburgh Paints (paint), Chevron Corporation (petroleum products), Coca-Cola Company (bottled carbonated drink), Wrigley Company (chewing gum), Kelly Moore Paint, etc. Here are some examples of process costing system calculations on how to allocate per unit cost to products:
Process costing system example 1
As one of the process costing system examples, let’s look at a supposed company, ABC Inc, that produces wire rods, that pass through multiple production departments. Assume, the casting department is the first department where the wire rods are initially created, and it incurs direct material costs of $50,000 and conversion costs of $120,000 (i.e. direct labor and factory overhead) in this department in the month of March.
If the casting department processes 10,000 wire rods in March, it means that the cost per unit of the wire rods passing through the casting department during that time period is $5.00 ($50,000/10,000) for direct materials and $12.00 ($120,000/10,000) for conversion costs.
If these wire rods are moved to another department for further work, say, the trimming department, the cost per unit allocated will be carried along with the wire rods into this department, where additional costs will be added.
Process costing example 2
Coca-cola is a carbonated drink bottling company that specializes in unique flavors. The carbonated drinks that the company produces pass through several production departments. Using this company as a process costing example, assume that during the month of May, $25,000 of direct material costs and $50,000 of conversion costs were accumulated by the filling department which processes 50,000 bottles.
This means that the cost per unit for the filling department in May is $0.50 ($25,000/50,000) for direct materials and $1.00 ($50,000/50,000) for conversion costs.
Let’s assume Coca cola carries out similar calculations for the labeling and packaging departments and discovers that it spent a total of $100,000 to produce 50,000 bottles in the month of May. It means the cost per unit will be calculated as $2 ($100,000/50,000).
Process costing system example 3
XYZ Inc makes paper products from wood pulp wherein raw materials go through a production cycle that ends with the production of identical reams of paper. Assume in the month of August, the company completes 150,000 reams of paper, spending raw materials total of $50,000, $70,000 in direct labor, and $30,000 for overhead. This means that in this process costing system example, the company incurred a total cost of $150,000 for the 150,000 reams of paper that it produces. Hence, the cost per unit will be calculated as $1 (total cost of $150,000/150,000 reams of paper).
Read also: Types of Profitability Ratios and Formulas
Advantages
- One of the basic advantages of a process costing system is that it is simpler to use compared to other costing techniques.
- Another benefit of a process costing system is that it creates a flexible production process
- One of the notable advantages of a process costing system is that it is cost-effective and requires less administrative effort compared to job order costing.
- Another advantage of a process costing system is that it helps in the quick assessment of costs for each production process and finished product; if overhead rates are specified, cost per unit can be quickly established at weekly or monthly intervals.
- The process costing system brings about uniformity to reports and makes tracking costs over time easier; the uniformity of the procedures of this costing system usually enables quicker submission of price quotes.
- Using a process costing system provides a clear picture of the costs associated with each unit of output which can be used to make decisions about production levels, pricing, and other aspects of a business’s operations.
Disadvantages
- One of the disadvantages of a process costing system is the possibility of costly mistakes building up in the production process.
- Since historical cost is the basis for the process costing system it is not totally reliable for future management decision-making.
- Another disadvantage of the process costing system is that average costs are the foundation of its process; average costs may not necessarily represent actual costs because a mistake in cost estimation in one process will definitely have an impact on cost estimation in the next processes as well as the cost per unit of finished and unfinished goods.
- The cost errors accrued in the production system are one of the limitations of a process costing system because direct allocation is not usually used in this costing system to allocate company expenses to products.
- In the process costing system, management accountants must calculate equivalent units (an estimation) which are reported as the work-in-progress inventory on the company’s balance sheet; if inaccurate, this can cause a distortion in the total of finished goods and also creates a difficult process for managing inventory.
- Process costing may give room for non-production costs to be included in the total process cost which can result in an increase in the cost of each item, thus, increasing the consumer product price.
- One of the disadvantages of the process costing system is its insufficiency for management objectives as a result of its lack of scientific foundation; when two or more items are produced using the same method, the total expenses are divided among them based on point-based weighting which results in an approximative cost that cannot be totally relied on.